How to Cut Thick Bevel Plate
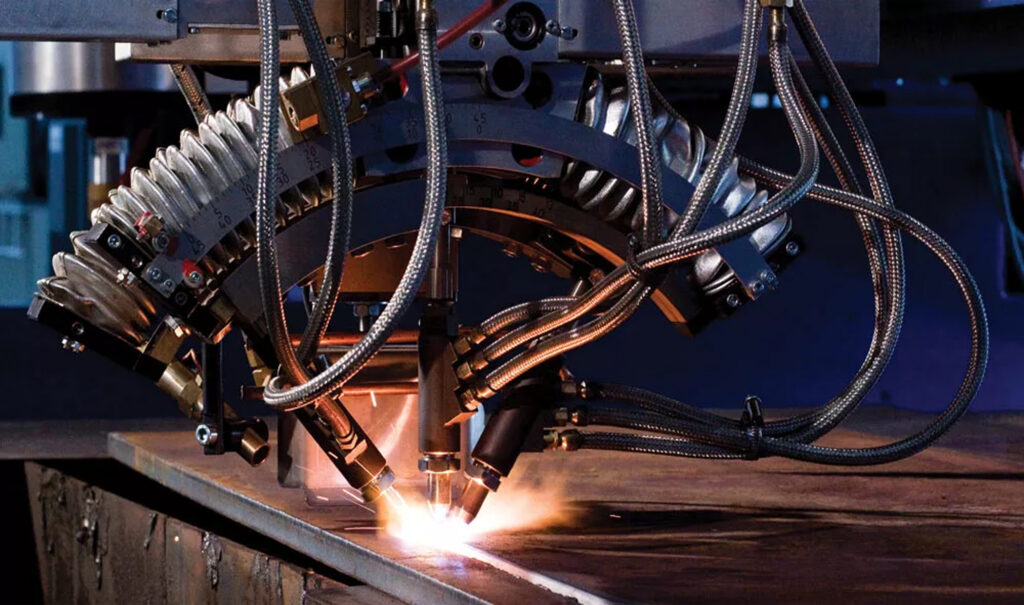
For fabricators looking to produce a K-bevel or more complex bevels, a triple oxyfuel torch that can program its own angles on the fly might be a good option. With this, the operator doesn’t need to stop the machine and change its angles. It’ll do it itself.
Prep and practice help fabricators get the most out of oxyfuel bevel cutting.
When processing thick and heavy plate, fabricators need to ensure that they are working with the right process and system. And while there are only a few options available, it’s still important to research and explore the different features and specifications to make sure that projects can be completed effectively and efficiently.
Several industries require bevel cutting of heavy or thick plate. Fabricators in the shipbuilding industry tend to know exactly what they are looking for when it comes to equipment, as the bevelling applications tend to be more on the standard side. However, the mining industry’s application ranges are more diverse, so those looking to bevel cut may have more options available to them.
Thick plate or heavy material can be expensive, so it’s important to get the cut right the first time. Fabricators should consider the following to make better bevel cuts.
Process
Plate thickness is one of the biggest factors that affect which process fabricators can use. Material hardness doesn’t really enter into this equation. There are a number of different ways to bevel cut, including both hot and cold processes.
When it comes to bevelling regular mild steel, plasma usually is a good option for plate that is 2 in. thick or less. Oxyfuel makes the most sense for plate thicker than 2 in.
However, fabricators looking to bevel stainless steel or nonferrous materials like aluminum need an extremely large power supply. Plasma is recommended in these cases, as some systems can bevel up to 4-in. stainless steel and aluminum.
Essentially, the thicker the material, the larger the torches need to be, and the more expensive the setup will be. That’s why, outside some specific applications, oxyfuel is recommended.
It’s really all about material type and application. Researching material and thickness limitations is a good place to start. It’s also a good idea for fabricators to reach out to bevel cutting system manufacturers to help guide them through their options.
System Requirements
The part configuration and complexity also will determine system requirements. For example, a triple-oxyfuel-torch setup is a great option. Each can be programmed for different angle requirements and move on their own. The system can shut off certain torches if a certain bevel-prep type is needed.
The greater the material thickness, the more robust the system needs to be. For example, an oxyfuel system that can process 4.5-in. mild steel needs to be able to handle the heat of processing plate for long periods of time. This is why thick plate requires less system automation. The process is just too hot for the automated system’s motors and components to withstand.
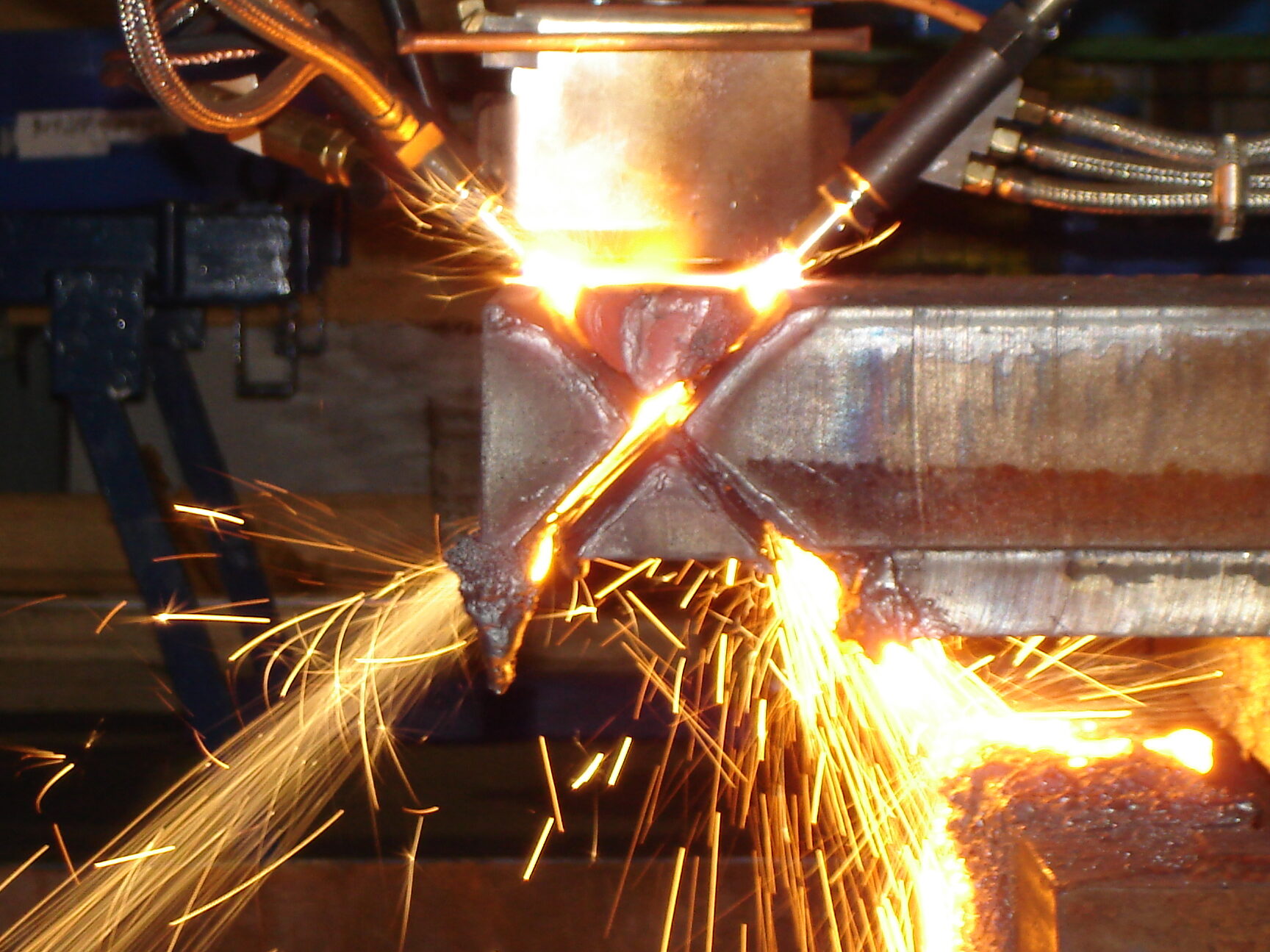
The bevel type also will determine the type of system needed. For fabricators looking to produce a K-bevel, which includes a bottom chamfer, a land, and a top chamfer, a system with one torch will require three separate passes on the same side of the plate. This will take a lot of time and increase the amount of heat generated.
For these applications, a triple-oxyfuel-torch setup that can program its own angles on the fly might be a good option.
With this, the operator doesn’t need to stop the machine and change its angles. It’ll just do it itself, increasing production. However, this setup is significantly more expensive than other options available that offer manual angles only. A manual system, which tends to be more robust, will require the operator to stop and make the changes from one side of the plate to the other, the machine will change out the weld prep type, and then the operator runs it again.
Cut Length
The thicker the material, the longer the cut length. Bevel cutting is not like straight cutting—if the plate is 2 in. thick, the cut length is 2 in. thick. In contrast, adding a 45-degree bevel in 1-in. mild steel requires cutting through 1.4 in. of material.
This is calculated by dividing the material thickness by the cosine of the cutting angle to get the true cutting thickness. So, cutting through 1 in. of material at a 45-degree angle adds 0.4 in. to the cutting length. Shops cutting 3- or 4-in.-thick materials, for example, may not realize that they are actually cutting through closer to 5 in. of material or more.
This will affect the amount of consumables needed to make these bevel cuts. Instead of using consumables meant for cutting 4-in. material, shops will need to use higher-capacity consumables to cut that extra material.
Cutting through more material, specifically with oxyfuel, requires a lot of oxygen, so shops should have a large oxygen tank available. Some fabricators underestimate how much oxygen is needed for a cut, and they run out mid-process because they failed to take that extra cutting length into account. Shops running three torches simultaneously will be cutting at a significantly slower pace, which requires more oxygen over time.
Preparation
Fabricators don’t always want to take the time to really dial in their parameters for their cuts. However, when working with thick or hard plate, especially some of the high-temperature alloys or exotic materials available that tend to be very expensive, some shops will purchase only what is required for a project and have no material to spare.
Fabricators should take the time to dial in the bevel angles and make sure the land height is the correct size. It can take time to do this in advance, and while some more experienced operators may not need that same amount of time prepping for bevel cutting, it is an important step to make sure the part comes out correct.
A lot of the systems available are very user- or newbie-friendly. However, with thick material, knowing the necessary pressures and what a good cut sounds like is a good place to start.
The part configuration and complexity also will determine system requirements. One torch with three oxyfuels included is a great option.
When it comes to thick plate or hard material, especially T1 steel, the data sheet can be an essential tool. Fabricators should check to see if the material requires preheating before cutting or if the cutting speed needs to be decreased. Preheat is an important step for hard materials as it moves the carbon off of the face of the steel molecule and back into its nucleus, making it softer to cut through. Essentially, preheating softens the material so it’s easier to cut through.
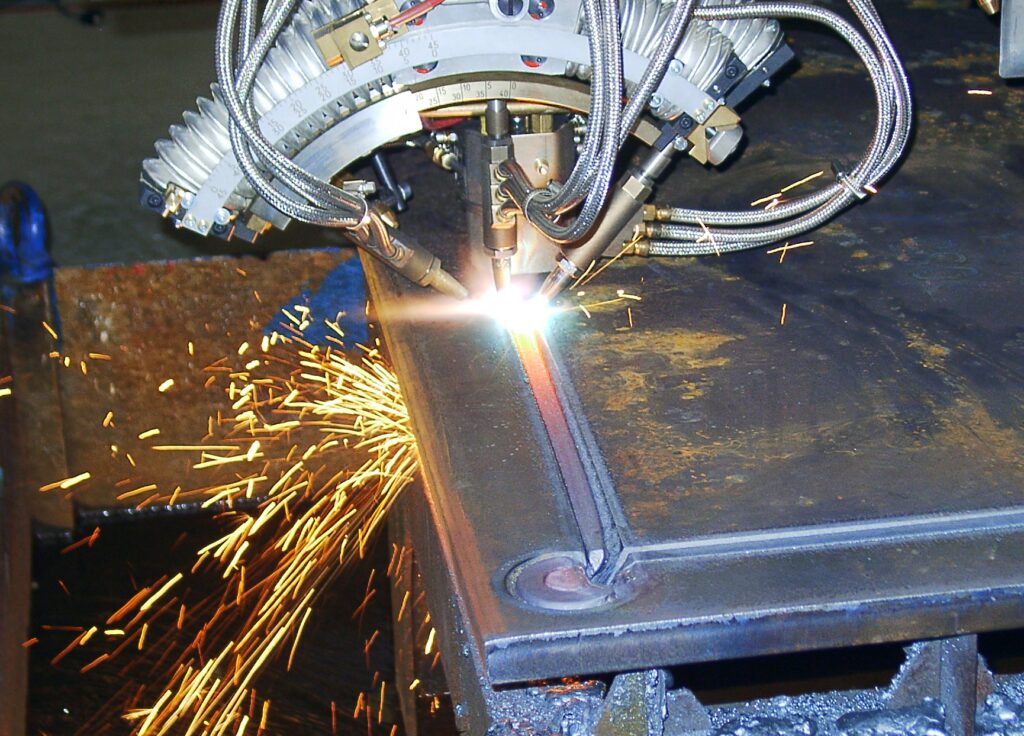
Fabricators should research their material and make sure their purchaser gets a material sheet from the supplier, which can serve as a helpful resource before cutting.
Taking time to ensure a proper setup, making sure the right consumables are available, and giving the operator the necessary time to make the cut is just good practice. Many fabricators tend to rush, especially with oxyfuel, which is a very slow cutting process that does not perform well when rushed. It requires proper cut height, gas pressures, and standoff distances. Rushing is never a good idea.
Practice
Rushing the process can cause programmers and operators to pull out their hair in frustration and worry. Especially for newer operators, worry can come from the fact that thick and heavy plate tends to be very expensive, and one mistake can lead to significant costs.
Practice will help an operator feel comfortable cutting. It will also provide them with a feel and context for how a good cutting process looks and sounds. With bevel cutting, experience is important, but taking the time to look at the parameters and actually seeing the process can limit the nervousness and stress an operator may feel.
Having a piece to practice on always helps.
Piercing
Hard and thick materials affect piercing ability. Piercing through the material can be difficult when bevel cutting. Once through, the operator can dial in the necessary speeds.
The operator needs to make sure the pierce is both effective and as short as possible. As a general rule of thumb and safety precaution, the lead-in to the part should be the same length as the thickness of the material.
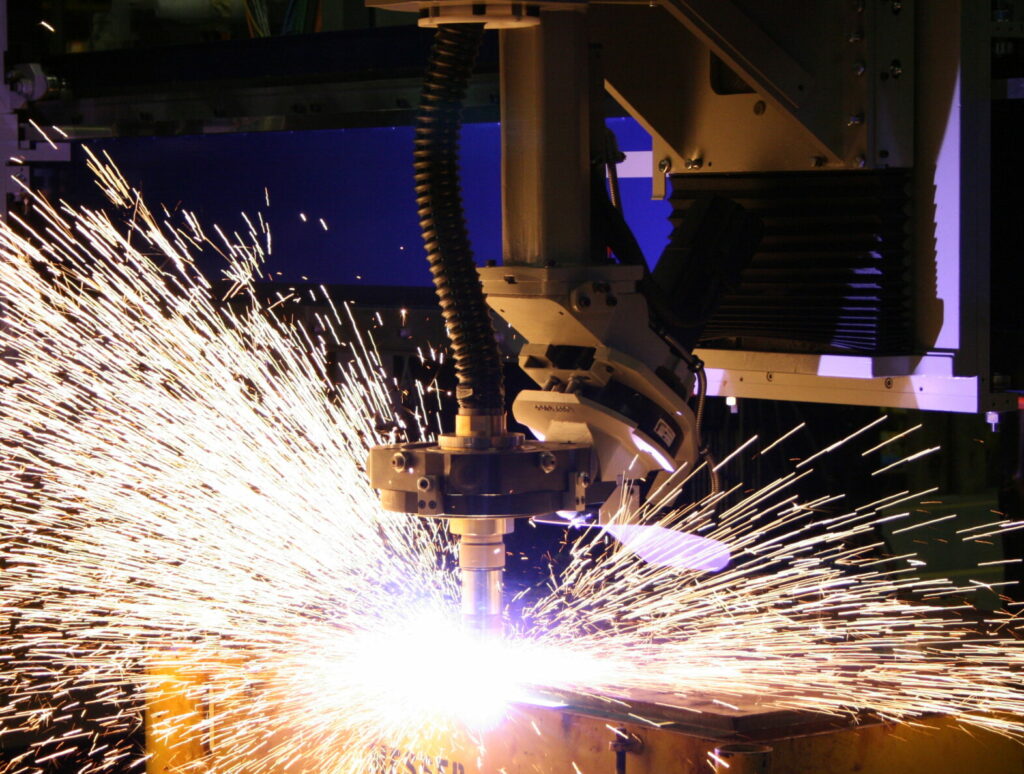
With 4-in.-thick material, the lead-in should be 4 in., but that takes up a lot of space. The trick is dialing it in to get through the material quickly. Piercing through the material in the shortest amount of space and time can help ensure that operators can get the greatest number of parts on the plate.
Article by: Alex Rood, Applications Engineer, Messer Cutting Systems
JUNE 2022 / CANADIAN FABRICATING & WELDING