It is Time to Consider Time
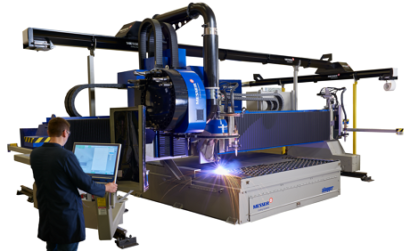
Menomonee Falls, Wi. – When companies invest in an automated plasma cutting machine, they expect to get a true cost-per-part savings. Yet the biggest qualifier is time, meaning the actual time it takes t.o produce the part or part nesting.
How long it takes plays a significant role in cost per part.
When companies invest in an automated plasma cutting machine, they expect to get a true cost-per-part savings. Yet some fail to consider the time it takes to create a high-quality, steel-cut part.
For equipment users, the main qualifiers in generating an exceptional piece part includes part accuracy, dross-free cuts, bevel angle, edge quality, hole quality, consumable wear, etc. Yet the biggest qualifier is time, meaning the actual time it takes to produce the part or part nesting.
Fabricators and machine operators instinctively understand that physically touching and moving parts around and off the table only adds time and labor costs. Due to the historic design of thermal cutting machines, parts are often cut and then relocated to another machine for additional machining processes.
The more you can do to a part with one set-up the more efficient your process will be. Manufacturers and processors have recognized this, and have begun demanding a faster, more accurate way of producing parts.
Messer Cutting Systems has responded to that challenge with the MPC2000MC, which features greatly enhanced drilling, tapping and milling capability, more robust design, and higher acceleration drives. The new drilling and milling chip high-suction vacuum system allows for a cleaner table surface and work area, preventing chips from flying off the surface of the table which increases operator safety. Also, there is a collection hopper for recycling steel chips.
Using the enhanced machining process allows you to drill, tap or mill critical internal features. External features are cut with the plasma or oxyfuel torch, without moving the part to another piece of machining equipment. This machine has a multiprocess capability, including plasma and oxyfuel cutting, bevel cutting, and marking, all coupled with OmniWin software.
The drill uses minimum-quantity lubrication so there ‘s no The drill uses minimum-quantity lubrication so there ‘s no need for a water table, which is coupled with the Slagger auto mated self-cleaning downdraft dry table for maximum performance. This modular-designed table is equipped to remove harmful smoke, dust and slag. The table features a blade unit that travels the entire length of the table, pushing small parts out of the table for collection, and cutting cleaning time from hours to minutes.
This article was published in The Cutting Edge / Fall 2018