Laser cutting is a fabrication process that utilizes a high-powered laser beam on a laser cutting machine to cut the material into various shapes and designs. The laser cutting process is suitable for cutting a wide range of materials including metal, aluminum, and stainless steel. A key benefit of laser cutting is that this process can generate precise and complex parts without any need for custom-designed tooling.
Several types of laser cutting machines are available, with each specific process producing parts with a high degree of precision, accuracy, and high-quality edge finishes. The laser cutting process generally results in less material contamination, physical damage, and waste compared with many other common cutting processes.
Messer Cutting Systems offers fiber laser (straight and bevel cutting) machines, fiber laser bevel cutting machine, fiber laser / plasma combination machines, and bevel cutting on Fiber laser machines, all of which are explored below.
What Are Laser Cutting Machines?
Laser cutting machines feature high-powered and highly accurate laser beams that are designed to produce precision cuts and clean etches on a wide gamut of materials.
These machines are usually used to cut materials in industrial manufacturing applications such as structural and piping materials along with metal plates. The laser beams on laser cutting machines are responsible for burning, vaporization, or melting excess material, resulting in precision-quality cuts.
Overview of Components of a Laser Cutting Machine
Laser cutting machines contain:
Laser cutting involves the usage of a laser cutting machine to create cuts, engravings, and markings. Although laser cutting machines vary across models and applications, typical machines encompass:
- A laser resonator assembly.
- Mirrors.
- A laser cutting head, containing a laser focusing lens.
- A pressurized gas assembly.
- A nozzle.
Additionally, the laser cutting process includes the following stages:
- Beam generation.
- Beam focusing.
- Localized heating and melting.
- Material ejection.
- Beam movement.
With the laser cutting process, each stage is critical. When each stage is executed correctly, a precise cut is achieved.
Beam Generation
The word “laser” is an abbreviated version of Light Amplification by Stimulated Emission of Radiation. This acronym ties “stimulation” and “amplification,” which are core laser generation principles. The laser resonator component utilizes spontaneous emission and stimulated emission in generating a high-intensity light beam that is spatially and spectrally coherent.
What Is a Laser?
An optical amplifier that converts energy into highly concentrated beams of light by stimulated emission of photons, or light particles, from excited matter. The unique properties of laser light enable more powerful, precise, and flexible processing within numerous industries and applications.
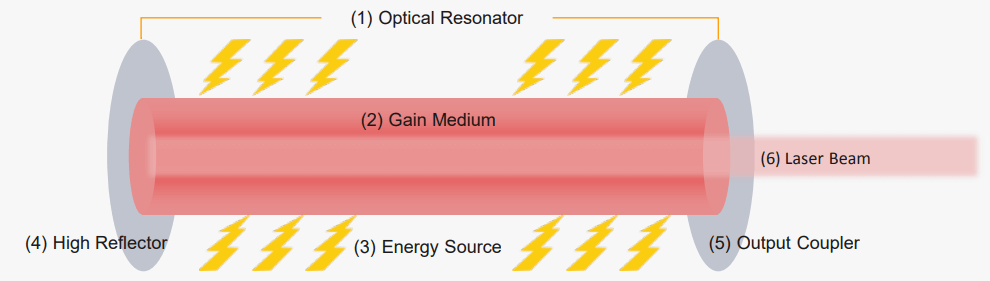
How a Laser Works
A laser consists of:
- An optical resonator, typically two mirrors between which a coherent light beam travels in both directions.
- A gain medium material within the resonator with properties that allow light amplification by stimulated emission.
- An energy source of light or electric current that excites atoms in the gain medium, known as pumping. Light in the gain medium travels back and forth between the two mirrors:
- The high reflector.
- The output coupler, being amplified each time. The output coupler is partially transparent, allowing some of the photons or laser beam to exit.
Types of Lasers
Lasers are often categorized by the type of gain medium (gas, crystal, fiber, semiconductor) but are also distinguished according to:
- The wavelength of operation (typically ~0.3 μm to ~10 μm).
- Pump energy source (electrical types of lasers).
Lasers are often categorized by the type of gain medium (gas, crystal, fiber, semiconductor) but are also distinguished according to:
- The wavelength of operation (typically ~0.3 μm to ~10 μm).
- Pump energy source (electrical discharge, flashlamp, laser diode).
- Mode of operation (continuous wave or pulsed).
- Power (typical milliwatts to kilowatts).
- Beam quality.
Beam Focusing
Optic Basics
The focal position is an important factor in achieving optimal cut quality. The location of the focal point is critical for every type of material you cut. The ProCutter moves the collimation lens, as the focusing lens is stationary, to adjust the focal position. The field in which you are working to attain the focal point is called the “depth of focus” or “range of focus.”
With nitrogen cutting, the cutter needs to be focused close to the bottom of the material so that the gas can assist in the removal of the material. This is referred to as endothermic cutting and is typically done with nitrogen assist gas at high pressures (10-plus bar).
With oxygen cutting, the cutter needs to be focused near the top because the laser and gas work together in what is called exothermic cutting, which involves typically low-gas-pressure oxygen cutting (less than 1 bar).

Localized Heating and Melting
Steel plate and other materials are heated and melted using either the energy of the laser or a combination between the energy of the laser and an exothermic reaction that amplifies the energy of the laser. Cutting with an inert gas like N2 uses only the energy of the laser to melt the material and eject it in a process known as fusion cutting while flame cutting uses O2 to create an exothermic reaction to enhance the energy of the laser with rapid oxidation.
Material Ejection
Material is ejected either by a high-pressure jet of inert gas in fusion cutting or a low-pressure stream of oxygen in flame cutting.
Beam Movement
The beam can be defocused to create a larger or smaller laser dot and kerf slot using beam shaping. This allows more molten metal to be ejected, enhancing the ability to cut thicker material.
What are assist gases and how are they beneficial.
Laser assist gasses typically are N2, O2, or air, with each having its own purpose. Pure N2 is used at a high pressure to eject molten material rapidly without affecting the cut edge. Cutting with N2 is typically considered the best quality and produces the highest cutting speeds but is limited in thickness. Air as the assist gas is used in a similar way to N2 but is less pure, containing only 80 percent N2 and 20 percent O2.
The higher O2 content can be detrimental in some cases and beneficial in other cases. Although air cutting comes with some compromises in quality when cutting mild steel, the addition of oxygen into the mix is of considerable benefit when cutting aluminum compared to pure N2. Oxygen is used to create a reaction with mild steel that amplifies the energy delivered by the laser and typically results in slower cut speeds but allows for thicker material processing compared with N2.
Contact
Messer Cutting Systems, Inc.
Laser Cutting Considerations
The laser type that is ideal for a laser cutting application largely hinges on the specific material that is to be cut. Other considerations, however, must be weighed when setting up a laser cutting machine for a specific application. These considerations may include focal spot, wavelength, beam mode, laser power, machine configuration, and material considerations.
Focal Spot
The laser beam is pointed through a lens and focused to a small spot of high intensity. The focal spot also referred to as the focus, is the point where the beam’s diameter is the smallest. The focus’ peak position for a laser cutting application depends on a range of factors. These factors include material properties and thickness, beam shape and mode, assist gas type, and focal lens state.
Wavelength
The laser beam’s wavelength is the spatial length of a single whole vibration cycle for a photon within the beam. The laser beam’s wavelength in part determines the material’s radiation absorption rate. This rate enables the material to be heated, melted, and vaporized in order to produce the desired cuts. Most fiber lasers today are optimized to cut at 1070 nanometers, near-infrared level.
Beam Mode
The beam mode is connected to how the intensity of the laser beam is distributed across the beam’s cross-sectional area. The beam mode affects the beam focal spot size as well as beam intensity. Beam intensity, in turn, influences cut quality. Usually, the optimal mode has a Gaussian intensity distribution (TEM00).
Laser Power
Fiber lasers used for metal cutting are typically in the 1- to 10-kilowatt range. Some fiber lasers even go higher, however, up to 15 to 20 kilowatts. More power does not necessarily mean thicker material cutting. Often, more power can generate faster pierce times, faster-cut speeds, and faster and thicker cutting, using fusion cutting techniques.
Machine Configuration
Laser systems always require an enclosure to protect operators from the harmful fiber laser wavelengths. Because of this, most systems have a shuttle or transfer table, so material can be loaded outside the enclosure and transferred in to commence cutting. There are also options available with enclosure systems, however, that automatically open and close to enable larger-format material to be cut.
Material Considerations
Fiber lasers can cut almost any ferrous or nonferrous metal such as mild steel, stainless steel, aluminum, brass, or titanium.
Pros of Laser Cutting
Laser cutting machines offer an attractive set of benefits to businesses:
- Fast speeds.
- Limited cleanup.
- Low operating cost for thinner metals.
- Material Handling options for fast and space-saving production on the shop floor.
Cons of Laser Cutting
Despite laser cutting machines’ distinct advantages, these machines have their drawbacks:
- They require a machine enclosure for operator safety.
- High cost for thicker materials.
- Significant capital investment.
Types of Laser Cutting Processes
Messer Cutting Systems offers several types of laser cutting machines, including fiber laser (straight) machines up to 20kW, fiber laser/plasma combination cutting machines, and (bevel cutting) on fiber laser cutting machines.

Fiber Laser (Straight)
Fiber laser (straight) cutting machines produce high-accuracy cuts with high efficiency and low heat input. Messer Cutting Systems offers 4kW to 20kW fiber lasers.
A laser beam is guided by a fiber cable on a fiber laser (straight) laser cutting machine. No adjustment between laser source and carriage as well as no purging gas is needed.
Offering a wall plug efficiency of as much as 30 percent, a fiber laser is significantly more efficient than many other types of laser cutting.

FIber Laser / Plasma Combination
Messer Cutting Systems’ fiber laser plasma combination cutting machine utilizes a fiber optic cable for beam delivery. It can also be used with the plasma process. By eliminating any need for mirrors, mirror maintenance such as cleaning, alignment and replacement are unnecessary.
The fiber laser process is three times more efficient compared with CO2 lasers, making use of a resonator unnecessary. Moreover, operational costs run measurably less because no laser gas is required.

Laser Bevel Cutting
Use of a bevel cutting machine requires precise knowledge of the laser machine and the cutting processes. Corners, lead-ins and run-outs have to be cut in a particular sequence so as to achieve the expected quality.
Bevel cutting also places sizable demands on the programming of cut parts. Special auxiliary functions are needed to set up the units for laser bevel cutting.
Alternatives to Laser Cutting
Businesses looking for high-quality cuts may also consider a couple of key alternatives to laser cutting: plasma cutting and oxyfuel cutting.
Plasma Cutting
Plasma cutting was developed for thermal cutting of materials that were not suitable for flame cutting such as high-alloy steels and aluminum. Plasma cutting is now also used for the economical cutting of thin, low-alloyed steels.
Messer Cutting Systems delivers on two types of plasma cutting options: straight cutting plasma and bevel cutting plasma.
Oxyfuel Cutting
Oxyfuel cutting is valued for being the most affordable process for cutting mild and low-alloy steel. As such, oxyfuel cutting is well-reputed as one of the most important production processes in the metal industry.
The oxyfuel cutting process is favored when the material surface that will be cut is made of mild steel and low alloy steel, with the material thickness being greater than 2 inches (50 millimeters).
This process is recommended if the plasma’s cut edge is considered to be unacceptable or if you are seeking a low-cost alternative.